Secret Benefits of Making Use Of Plastic Shot Molding in Manufacturing
Plastic shot molding has actually emerged as a critical technique in the manufacturing field, supplying a variety of advantages that dramatically boost production procedures. Notable benefits include amazing manufacturing performance, the capability for complex layouts, and a beneficial price framework that appeals to organizations of all sizes.
High Manufacturing Effectiveness
One of one of the most significant advantages of plastic injection molding is its high manufacturing effectiveness, which can cause the quick production of thousands of similar parts within a brief timeframe. This performance is greatly associated to the automated nature of the injection molding process. As soon as the initial configuration and mold creation are completed, the production of parts can be scaled up considerably without a corresponding boost in labor prices or time.
The procedure commonly entails heating plastic pellets up until they melt, injecting the molten material into a specifically made mold, and enabling it to cool down and strengthen - Plastic Injection Molding. This cycle can be finished in mere secs to mins, depending on the complexity and dimension of the component being created. As a result, producers can accomplish high output rates, making plastic shot molding an ideal choice for mass manufacturing
In addition, the capability to create big quantities constantly guarantees reduced device costs, making it an economical option for companies. This manufacturing efficiency not only fulfills market demands quickly yet likewise enhances the total competition of manufacturers in various markets. Plastic injection molding continues to be a recommended approach for high-volume production applications.
Design Flexibility
The abilities of plastic shot molding extend past high production performance to incorporate significant style flexibility. This production procedure enables designers and engineers to produce complicated and complex forms that might be challenging or impossible to attain with various other approaches (Plastic Injection Molding). The ability to quickly adapt and change mold and mildew styles means that producers can rapidly react to altering market demands and innovate brand-new item layouts without comprehensive retooling
Moreover, plastic shot molding supports a wide variety of materials, including different thermoplastics and thermosetting polymers. This selection makes it possible for the manufacturing of components with distinct buildings, such as enhanced strength, lightweight features, or details thermal and electrical qualities. Furthermore, the process permits the integration of numerous features into a solitary part, minimizing the need for setting up and decreasing potential factors of failing.
The precision of injection molding likewise ensures that parts are created with tight tolerances, enhancing fit and function. The flexibility to generate little to large sets successfully further underscores its adaptability, making it an excellent option for both prototyping and large-scale production. On the whole, layout versatility is a keystone advantage of plastic shot molding, driving development in various industries.
Cost-Effectiveness
Cost-effectiveness stands out as a significant advantage of plastic shot molding in production. This process permits the mass manufacturing of high-grade plastic elements at a relatively affordable each, particularly when contrasted to various other producing techniques. The efficiency of injection molding exists in its ability to create complicated shapes with minimal waste, optimizing product use and reducing total expenditures.
Furthermore, the rate of production is an essential aspect in cost-effectiveness. When the first mold and mildew is produced, the time needed to generate each succeeding part is significantly decreased, leading to enhanced output and faster turn-around times. This quick production capacity not only meets high-volume needs yet additionally minimizes labor prices, as automated systems can handle much of the procedure.
Moreover, the durability and long life of injection-molded products add to their cost-effectiveness over time. These parts usually require much less upkeep and substitute, resulting in lower lifecycle costs for suppliers and end-users alike. In summary, the cost-effectiveness of plastic shot molding makes it an appealing choice for services looking for to boost their production performance while keeping item quality.
Product Versatility
Material convenience is a trademark of plastic injection molding, allowing producers to pick from a broad selection of polymers that fulfill certain efficiency needs. This flexibility enables the manufacturing of elements tailored to various applications, ranging from automobile components read to consumer products.
Frequently utilized products include acrylonitrile butadiene styrene (ABDOMINAL), polycarbonate (COMPUTER), and polypropylene (PP), each offering distinct residential properties such as effect resistance, warm tolerance, and chemical stability. Manufacturers can choose materials based on features like stamina, weight, and thermal stability, guaranteeing completion product meets aesthetic and practical requirements.
Furthermore, the capability to combine various polymers via co-injection strategies further boosts product flexibility. This permits the development of multi-layered parts with unique qualities, such as soft-touch surface areas combined with inflexible architectural components.
In addition, developments in recycled and eco-friendly materials are increasing the choices readily available, straightening with sustainability goals in manufacturing. On the whole, the varied material choices in plastic shot molding empower makers to innovate and enhance their items, facilitating the development description of extremely specialized and competitively advantageous remedies.
Boosted Product Toughness
Improved item sturdiness is among the considerable advantages supplied by plastic shot molding, as the manufacturing process enables for specific control over material buildings and component style. This accuracy makes sure that the last items show boosted mechanical strength and durability, which are critical aspects in a range of applications, from customer items to commercial components.
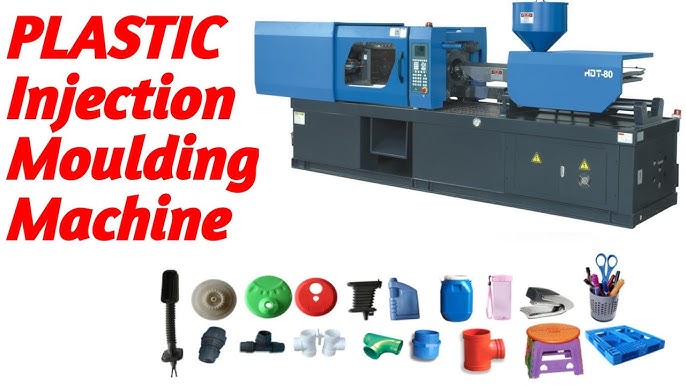
In addition, the elaborate geometries possible with injection molding make it possible for the development of components that can stand up to stress and stress far better than standard production approaches. The consistent wall density and lowered product waste also contribute to the general honesty of the product, decreasing the chances of failing during its moved here lifecycle.
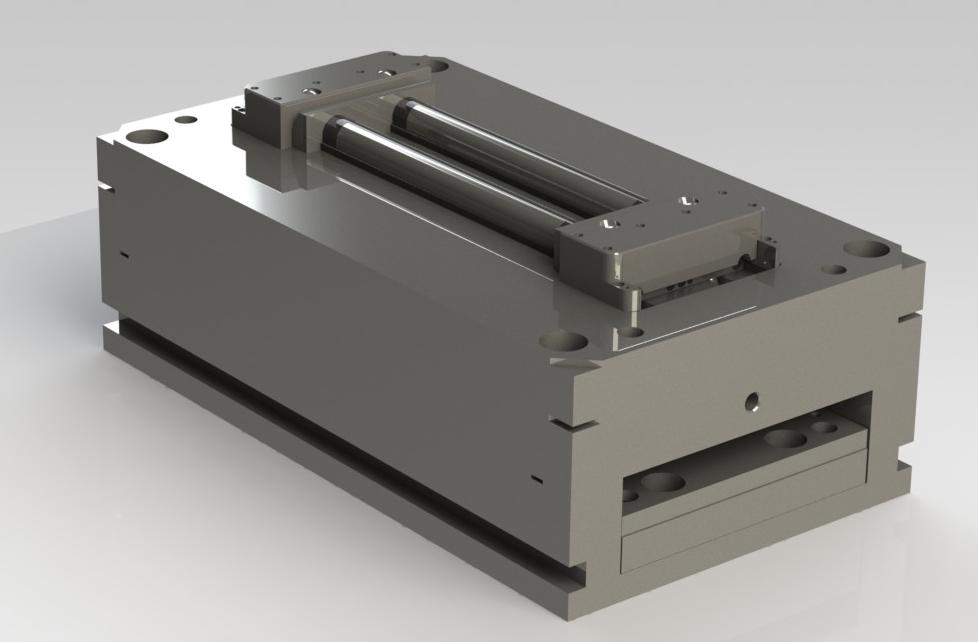
Verdict
In conclusion, plastic shot molding offers significant advantages in manufacturing, consisting of high manufacturing efficiency, layout adaptability, and cost-effectiveness. These aspects jointly establish plastic injection molding as an optimal solution for mass production applications, attending to the dynamic demands of contemporary production settings.
Plastic injection molding has emerged as an essential strategy in the production industry, providing a variety of benefits that dramatically boost manufacturing processes.One of the most considerable advantages of plastic injection molding is its high manufacturing performance, which can result in the fast manufacturing of thousands of identical components within a brief duration. Plastic Injection Molding.The capacities of plastic injection molding expand past high production efficiency to encompass considerable style flexibility.In final thought, plastic injection molding provides significant advantages in manufacturing, including high production efficiency, design adaptability, and cost-effectiveness. These elements jointly establish plastic injection molding as an ideal remedy for mass manufacturing applications, dealing with the vibrant demands of modern-day manufacturing settings